A hook on a pulley for some sort of crane or something. Based on dimensions given in an old, undated book from Spain of technical drawing exercises.
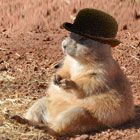
Best posts made by Dave R
-
Hook on a Pulley
-
A Recent 3D Printing Project
This is a heel strap for a wheelchair to prevent the user's feet from sliding off the foot plate. It's designed to install easily with no tools required except scissors to trim the strap to length. The clips with snap on covers are 3D printed to fit off the shelf polyurethane toothed belting.
From the SketchUp model.
Partially assembled.
Temporarily installed on a chair. Ignore the dog hair.
-
SketchUp's AO and Vray
Combined a Vray render with an AO export direct from SU24.
-
Vintage Look
Experimenting with creating a vintage illustration style for my SketchUp models. The flywheel is based on dimensioned drawings in a textbook from 1897.
-
Another Machinist's Model of a Steam Engine.
This one is called Lady Stephanie. I don't know who the real Lady Stephanie was but if she was anything like this engine, I'm guessing she was kind of ornery and hard to please.
-
RE: Another Machinist's Model of a Steam Engine.
After putting her aside I did another engine today. This is a a little crankless engine.
-
"Watt" Micrometer
A model of what is probably the first micrometer ever made. It's dated England about 1776 and attributed to James Watt although evidence shows it likely wasn't made by him.
A larger version of this image is available here.All the screws are made and holes threaded. 28 component definitions, all solids.
-
RE: Another Machinist's Model of a Steam Engine.
Funny guys!
And here's another one. A little 4-cylinder oscillating engine. As usual, all base level components are solids.
-
A Mahogany Lowboy
This is from a model I initially made 11 years ago for shop drawings. I pulled it out recently to do a bit of refining in SU2025.
Latest posts made by Dave R
-
RE: SCFLicense: Extension Licensing on Sketchucation
@aenc_randyc said in SCFLicense: Extension Licensing on Sketchucation:
I have FredoCorner from 2023.
Make sure you have installed the latest version of the Sketchucation ExtensionStore, FredoCorner, and LibFredo6.
-
RE: SCFLicense: Extension Licensing on Sketchucation
Are you sure you didn't purchase a license FredoCorner instead? Confusing Round Corner and Fredo Corner is the usual reason for the message you are seeing. Look closely at the license information you received.
-
RE: Another Machinist's Model of a Steam Engine.
Thank you!.
Here's an animation I did as an experiment with scenes, native materials, and Vray.
-
RE: Model for 3D print will not make solid (SU 2015)
You're welcome.
@jgb said in Model for 3D print will not make solid (SU 2015):
I never knew about using "tab" in Solid Inspector 2.
It's a good idea to check out the message line at the lower left of the model window whenver you start a tool.
@jgb said in Model for 3D print will not make solid (SU 2015):
Next model I will try using meters instead of centimetres. Just that 10:1 is easier to work with than 100:1 as I have to visualize the model against a ruler to get some sizing correct.
You misunderstand what I told you. There's no need to deal with 10:1 or 100:1 at all. Set the model units to meters. Read millimeters off your ruler and just enter them without doing any math at all. If you measure 15 millimeters on the ruler enter 15 in SketchUp. It'll go in as meters but you don't need to do anything with that. When you export the .stl export it with Model Units set to meters. When you open it in the slicer it'll be in millimeters and you don't have to do anything as far as the scale goes.
Here's another example. Model in SketchUp with units set to meters. The screws are M6 but the threaded part is modeled at a hair under 6 meters in diameter.
And the 3D printed parts.
The M6 screws fit into the tapped M6 holes just like their commercially made metal counterparts would.
@jgb said in Model for 3D print will not make solid (SU 2015):
Alternatively, just open the group or component and activate the tool. Saves you from jumping in and out of the object while editing.
Doesn't work for me. What am I missing here?
I guess you'd have to ask Thom Thom about that one.
-
RE: Model for 3D print will not make solid (SU 2015)
@jgb said in Model for 3D print will not make solid (SU 2015):
Solid Inspector never flagged those "overlapped circle" edges, and I never noticed them either.
Except for the two missing faces at the corners where the horizontal opening is, the other edges were not preventing the object from being solid so no reason for Solid Inspector or Solid Inspector 2 to identify them. The reason I mentioned them is there's no reason for those edges to exist in the first place and they could later cause you problems.
@jgb said in Model for 3D print will not make solid (SU 2015):
"Tab" doesn't work in SU 2015,
It should. Are you using Solid Inspector2?
@jgb said in Model for 3D print will not make solid (SU 2015):
As for model scaling, I draw in centimetres, print in millimetres (10:1).
Do whatever you want. Had you been modeling in meters you likely wouldn't have had any of the surfaces borders (missing faces) to fix in the first place.
@jgb said in Model for 3D print will not make solid (SU 2015):
Any idea on the surface borders and internal face edges?
I showed you where they are.
Here, again.
-
RE: Model for 3D print will not make solid (SU 2015)
@jgb said in Model for 3D print will not make solid (SU 2015):
I normally make front/back faces the same, as colour differences show up along edges.
That's OK for output but it leads to sloppy modeling if that's your working style.
@jgb said in Model for 3D print will not make solid (SU 2015):
Solid Inspector correctly orients the faces.
Sometimes it does. Sometimes it doesn't.
@jgb said in Model for 3D print will not make solid (SU 2015):
When I went back to the model, I cannot see any difference in front/back face colours. How did you see that? How can I fix that?
I selected a style with the default blue back face color.
@jgb said in Model for 3D print will not make solid (SU 2015):
But when I am in the throes of design I keep the part in default "no" colour both sides and if needed, just colour the component as a whole.
Personally I prefer to keep the file neat as I go even when I'm in the "throes of design." It's generally quicker and easier to deal with exposed backfaces when and if they occur. With the right work flow you should rarely need to stop and fix face orientation anyway.
-
RE: Model for 3D print will not make solid (SU 2015)
Poking around a little more I see you have set the back face color to match the front face color. That's a lousy workflow. It makes it more difficult for you to see holes (missing afaces) and it makes it impossible to detect incorrectly oriented faces. Face origintation is especially important for 3D printing because that tells the slicer which side of the face is the print media and which side is air. In your model you have a number of incorrectly oriented faces. Make the back face color significantly different from the front face color. If you have set the back face color to white for your template you should deal with it and create a new template.
-
RE: Model for 3D print will not make solid (SU 2015)
Highlight one of the error lines and tap Tab to zoom in to the error. Tap again to go to the next one. Rinse and repeat.
BTW, you should clean up your model a bit. Looks like you had overlapping circles on that large central hole.
When I model for 3D printing I model as if millimeters are meters with Model Units set to Meters. I export the .stl file with Export Units set to Meters and open in the slicer as Millimeters. No tiny face issues which is the reason for the errors on the edge of that large hole.
Example: This is the SketchUp model.
And the 3D print.
It snaps onto a 19mm diameter tube. -
RE: Strange corners
Hard to say from just a single image. What orientation was the model in on the bed? What material?
Advertisement