But does he wear them??
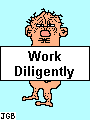
Posts made by jgb
-
RE: Zoom Extents does not work if Hide Components is ticked
-
RE: Zoom Extents does not work if Hide Components is ticked
See? This one is real and not "imagined".
So, how do I collect my Tee Shirt??? -
Zoom Extents does not work if Hide Components is ticked
Please see this topic for the details of what led up to this bug report.
http://groups.google.com/group/sketchupsuggestions/browse_thread/thread/85ebdb51af3ad325?hl=en
In essence the following has been determined to be a bug in SU6 and SU7;
When using Context [RightClick Zoom Extents] to zoom onto a selected object, the following was noted;
Selecting a top group and [Rt.Clk Zoom Extents] will zoom onto the object as expected.
If [View][Component Edit][Hide Rest of Model] is set to OFF/unticked (ON layers are ghosted during edit) [rt.clk zoom ext.] will zoom onto selected sub elements as expected.
If [View][Component Edit][Hide Rest of Model] is set to ON/ticked, (ON layers are invisible during edit) it
does NOT zoom on sub elements. It will zoom onto the global origin beyond the view of the selected object.Wo3Dan confirmed this by finding;
Even when ALL geometry is on layer0 the 'Zoom Extents' does not seem to work on selections within any editing context in groups and/or components when 'Fade rest of model' is checked. The result is always the current global origin in the middle of the screen.
Joel G Berson (jgb)
-
RE: Fresh Start to an SP Tutorial
@wacov said:
Don't see why no-one else has replied
I'd be happy to help, I've got good general knowledge of SP and I know some workarounds for problems; I don't have a huge amount of spare time but this is something I'm interested in; Smaller mini-tutorials for more specific/advanced stuff is what I'd like to do.
My guess is that nobody really wants to devote the effort. Like I said, it is not a trivial task.
As for advanced stuff mini's, we need to document the fundementals first. Take Curbs work and flesh out some more details on the basic joints and settings. Then carry on where he left off with the remaining joints. At that point we can get into advanced stuff like linking different types of joints and how-to's on some of the fancy stuff we've all seen, but can't figure out how to do. -
RE: Fresh Start to an SP Tutorial
@shareck said:
ok. i've seen models on the warehouse that have a motor with reverse function controlled by a single controller. |Still i cant figure out how to make such a motor. Please. Prepare a tutorial for me
Best to repost this as its' own topic. The how-to you get will form part of a tutorial, if it ever gets going.
-
Fresh Start to an SP Tutorial
(Transfered from "How can we help out?" topic in
"http://groups.google.com/group/sketchyphysics/"
on Chris Phillips recommendation.) jgbThere have been several attempts at properly documenting SP. So far
the incomplete but best effort is by Curbs. I tried, but Curbs
outclassed me by a long shot, so we sorta joined forces, till I had to
abandon my efforts due to other commitments, and my inability to wrap
my head around some fundamentals of SP. (That's about me, not SP.)So, what I'm saying here is, don't underestimate the complexity of
documenting SP. It is a great program with great possibilities, but
it IS complex. I would suggest setting up a specific SP tutorial
forum strictly for collaboration, continuity, and division of labor.
One person cannot do it all, unless it is a full time endeavor and that
person knows SP inside out. Chris can only help so much, as coding is
his forte, not tech writing, by his own admission. That is fair, as
some are great coders, and some are great tech writers, and it is very
rare both are one person.I can help as well. My main experienced strength is project
planning. If a bunch of you that want to participate in a thorough
tutorial covering all that SP can do, then let's meet here and decide
on a format (See Curbs tutorial as a prime guide) and define the
various SP tools and processes at play, then divvy up the work.This is NOT a trivial task, and it will take weeks if not a few months
of committed coordinated work and testing/proof reading.It also means using a single forum as the Tutorial meeting room, and
not opening new threads to ask Chris a question. We all need to be
"on the same page" so to speak. And I think Chris should be coding
not dancing between forums on this matter.Also, as has happened before, this will not be an ad-hoc forum where
non-tutorial questions are answered. They tend to hi-jack a forum
once people see all the "experts" congregating.So let those that are interested reply here, and we will see where it
goes.jgb
-
RE: [SP2]Basic Tutorial Posted (Moved & Improved) 5/11/08
Absolutely top notch addition to the tutorial.
The new sections were full of "I didn't know that!!!" and now I gotta play with this.
One minor note, a very common spelling error, in section 6, 1/2 way down, the sentence "NOTE: These blocks are SEPERATE groups" is spelled SEPARATE. I do it all the time.
Also I have not lost interest in this "project". I have been sidetracked back to an unrelated (to SU or SP) project, a patent application which is now in final review before the USPTO application, and there is a lot to do in that. The application is about 75 pages, and part is in a language (legalese) I don't work well in. To quote Arnie, "I'll be back" in about a week or 2.
-
RE: [SP2]Basic Tutorial Posted (Moved & Improved) 5/11/08
Your 5 minutes is my 5 hours, if I succeed.
Yes I knew about the Joint layer, just didn't occur to me.
Thanks
jgb
-
RE: [SP2]Basic Tutorial Posted (Moved & Improved) 5/11/08
Chris
It's amazing what the hand of the master can do. Thanks.
Last night I looked at a few working models (mainly the steam engine) and came to realize that jointed objects should touch for stability. I deliberately kept them apart, to preclude interference. I learned that when my ball joint at the apex of the drag strut jammed against the bogie early on, and when I was swinging the gear doors through the outer skin. I opened the joint separation clearances, and the interference problems went away. I guess that gapping now has to be done more judiciously.I was about to change my LG model to tighten the hinge and servo joints, and your edits show I'm on the right track. Based on that revelation, I'm going to experiment with large disks at the joints (to be hidden) just to act as stabilizers. Yet that confuses me as Curbs demo has very widely separated joints, and his is very stable.
Adding mass is a surprise. I noticed you placed capsules on some parts. Any reason why those and not just a simple cube (to be hidden)? What governed the size?
I noticed the servo joint is visually gone, but its physics remain. I know we can delete a joint group drawing, and it still works, but with the joint gone, there seems no way to delete it if needed, or see it for reference. Did you remove it for any reason?
Anxiously awaiting the new SP version. Any idea on its release date?
Curbs.
Thank you as well for the demo.As far as overthinking the problem, I am very prone to that. The old planner in me. I'll spend an hour planning how to do a 10 minute job.
However, my process as stated was the result of about a dozen trial-and-error exercises, mainly on the failed LG door hinging. I have the paper trail to prove it. It is very conceivable I led myself up the proverbial garden path, but I tried all combos of grouping and attaching to get to there, all starting from scratch (deleting the joints). Having little experience in SP, I may not know the better way, and discovery may or may not show me that way. I used your tut as a starting point, and it worked in some cases, but not all. That is how I found that servos and hinges attach a bit differently.
My next planned trial was to do as you suggested, draw everything, attach the joints all at the same time, then group them in a logical order, also, I surmised from the free end back to the base, but I ran out of time yesterday. It seems we think alike in many ways; it just takes my old bones longer to get there.
And so far, I have only played with servos, hinges and used a ball joint and "U"joint a very few times. I've had zero success with sliders for what I want to do with them.
I also came to the conclusion, that I had to tighten my joints (see above to CP).
Yet your right hand demo shows a wide joint separation, but it is stable, with no bounce or dislocations at extreme ends. Why are mine so loosey-goosey?Have a good trip; it's time for me to play.
jgb
-
RE: Steam Engine- Working Model
Seeing that brings tears to my eyes.
I am having so much difficulty getting my landing gear demo to work properly.
How did you achieve the joint stability? Mine is all loosy-goosy and unstable.
jgb
-
RE: Just an idea
SU has a "bad habit" of showing bits of stuff thats behind a face as you zoom away from it.
In several of my models, I have a face that is an inch thick (actually 2 faces an inch apart) and there is some structure attached to the inner face. When I look at the outer face from a short distance, the face is clean. As I pull away, ghosts of the structure an inch away start to appear on the outer face. They go away as I zoom back in. These aren't hidden lines either.
So I suspect that is what we are seeing in that exquisite rendering, and it being transparent, the ghosting is more appearant.
jgb
-
RE: An SP newbie, trying to write a tutorial.
For those of you who are following, I have a Landing Gear Demo version 3 and associated notes now posted in the "Basic Tutorial Posted" topic. http://www.sketchucation.com/forums/scf/viewtopic.php?f=61&t=9115
I put it there as it now is part of my contribution to the tutorial Curbs is writing instead of me.
jgb
-
RE: [SP2]Basic Tutorial Posted (Moved & Improved) 5/11/08
OK, here it is. Incomplete, but the main part is working.
Turn layer 1.5 A/C Outer Skin visibility off to see the thing working.
In this version 3 of the demo, there are several significant changes over version 2, aside from getting it to work.I deleted the documentation layer. It just got in the way, and was a bear to update.
The LG door is in 2 parts, and is bigger. The 2 part is really the basic design for the whole thing. My previous demos were 1 piece, because they were a demo. Now I need it in 2 pieces to complete the demo, and this demo has proven to be of more value than I expected. It forced 2 major design changes to the base design.
I am having a lot of frustration properly hinging the 2 doors. I got it working on Friday, but I made a change to the doors, and never got it working the same again, so for Ver 3, they simply drop off.
What I want in the next demo is for the top door to hinge from the skin at its top edge, and the bottom door to hinge from the bottom of the top door. There will be a set of actuation struts connecting the doors to the bogie with various joints, so they open as the bogie extends. I noticed that if the doors simply hang there, they interfere with the bogie and the bogie goes unstable. So to prevent that, I replaced the upper hinge with a servo so the doors partially opened under control, and there was no interference if I opened the doors before trying to extend the bogie. Not being able to keep the bogie up when starting the run (it goes 1/2 way down), I adjusted the door servo to fully open on run start by setting the min/max angle. That's when I shoulda saved it and posted it here. Nope; I just had to try something. It all blew up, and I have not been able to get back to that point since.
Changes to the bogie.
The biggest change was required (and it will be incorporated into my airplane landing gear model) because the bogie is pushed out (red axis) during its motion by the drag strut. At first the excess flexibility in the joints hid this fact, until I got up close to see what was happening. I had to change the top pivot to a 2 joint affair. Can't use a "U"joint or ball joint, as there is nothing strong enough in "real life" to take the kind of loads this LG will impart on that joint. There is such a joint, called a "spherical bearing", but not that big, nor do they have the range of motion needed. It had to be 2 hinges on the red and green axis. So now the bogie can swing free, controlled by the drag strut. The extra lobe on the back of the part is for the up/down lock, to prevent the bogie from moving while handling the landing shock and loads.I had to put the green axis hinge mid point in the part, to avoid perception problems looking at the whole thing. I know the actual joint group does not have to be on the part, but on the joint line common to the 2 parts, but it looked real weird to put it offboard the bogie. And yes, I can turn off the joint layer visibility if I have to.
So here is what I've discovered.....
For the tutorial......
1- Do not attempt to edit a part with a joint connected to it, if the edit changes the part shape, or disturbs the joint line. Delete the joint, edit the part, re-attach the joint.
2- Make sure you can see the joint within the group. If you bury the joint inside the part (as I first did with the top green axis hinge) and you cannot see it, you cannot attach it properly, and the joint will fail. That is why there is a "cutaway" in the top of the bogie.
3- So far I've only played with hinges and servos. They attach differently!
A hinge is placed on the moving part. Then the hinge is jointed to the moving part and grouped to the moving part. Then the hinge is jointed to the parent part.
A servo is placed on either part. It is then jointed to both moving and parent parts. DO NOT group the servo to either part. I have not yet experimented with putting a servo between 2 moving parts. Should be hair pulling fun.
4- Make sure to shape all the relevant parts correctly. Make sure to shape the grouped jointed part the same shape as the part alone. Yes, you have to set shape twice.For Chris........
1- Is it possible to tighten up the joint flexibility? I noticed that I had severe dislocations and joint distortion at motion extremes which seems to be caused by the sheer "weight" of parts hanging from the joints, plus a lot of bounce. That also happens when there is a motion interference. When I changed the SP gravity to .1G, the bounce and distortions lessened significantly. Joints should be quite rigid except along the motion axis.
2- (Asked before) Can we get a "start" angle setting for the servo, between the min & max angles?
3- Also on the servo, when I get very close to the zero (left) setting on the control, the servo spins uncontrollably. At the 1 (right) setting, it just stops as expected.
4- Could you make the [ESC] key equal to reset?I got more, but this is enough for now.
jgb
Landing Gear Demo, bogie extension/retraction under control.
-
RE: [SP2]Basic Tutorial Posted (Moved & Improved) 5/11/08
I went through your update.
You left out 2 important steps.
1 - You need to Joint Connect the joint to the moving part before you group them.
2 - You need to set the SP shape of the joint/part group as well, and to the same shape as the part alone was set to.I tried it "by the book" and it did not work. When I did the 2 extra steps above, it worked.
BTW, my LG demo is working, at least the bogie comes down as commanded. I had to redesign the upper hinge joint for extra flexibility to get it to work without distortion. I'll post it later in a separate note, and detail what changes, and problems I had making it work thus far.
Still playing with the LG doors. I had them swinging free, then opening with a servo, but I made a minor edit, and the whole thing blew up. Trying to get back to the almost working state first.
jgb
-
RE: Just an idea
An extension to this good idea, is perhaps a "frame step" button for SP. Click on [frame step] and each mouse click or [enter] key advances the SP run action, one (or user defined) frame at a time. Then you can easily take a snapshot at any stage of the scenes progress, at any view angle or zoom, assuming scene creation will work during an SP run.
jgb
-
RE: An SP newbie, trying to write a tutorial.
I think I am getting the hang of it.
I did some editing of the LG door and surrounding airplane skin, to open up the opening. Then I drew the drag struts and connected them to the fuselage with a hinge, and to the LG bogie with a ball joint. Worked FIRST TIME!!!!
Then SU crashed, and I had to start much of it over from the autosave copy.
SU has been crashing a lot lately as I am playing a lot with joints. It seems to crash about 4 hours into my playtime. I've now learned if SU crashes, I need to reboot my PC to clear the crap out of RAM, otherwise SU will crash again soon after reloading the file.
When playing with SP, SAVE OFTEN!!!! Or keep the autosave running on short intervals.Anyway, it's NOT posted here yet, because I had a dimension error in the strut, so it looks real weird when running. But it does do what I want it to do. I'll fix that and post it later.
My process flow as above seems to work.
Rule #1: Best to put the joints on the moving parts, as Chris suggested. I've tried both ways now, and the new way is far less problematic as you get deeper into the model.
Now the following may not be entirely true for the newer capsule joints, but I haven't had time to test them yet.
Step 1) Make your moving part, and group it, including any other parts attached to it.
2) Set the shape of the moving part appropriately.
I have found that Convexhull is great for anything that cannot be adequately defined by the geometrical shapes (box, cylinder, etc)
3) Attach a joint to the part.
3) Connect the joint with the Joint Connector, first clicking on the joint, then CTRL-Click on the moving part.
4) CRITICAL: Group the joint and the moving part group.
5) With the Joint Connector, click on the joint and then CTRL-click on the stationary group.
Do not group these.If your moving part is connected at the other end to another moving part (chain linked), you have a choice. You can put the joint on either part.
If you chose the other part, do as above steps 1 - 5.
If you chose to put the joint on the first moving part, you need to UNGROUP (explode; not edit) the part and the first joint, place the second joint, connect the second joint to the part, then regroup both joints and the part. Only then connect the second joint to the second part, but DO NOT group them.
This way, the whole assembly can be as complex as you want, and the joints/parts are easily edited. Again, if you have a main part with other moving parts hanging off it, put all the joints on the other moving parts hanging off it.
One other thing I have noticed. If you need to edit a part where the joint is attached, ie: lengthen it at that end, explode the joint/part group, DELETE the joint, make the edits, and then replace the joint, regroup and reattach as new. Editing a part which may move the joint in place will cause problems.
More later. I feel a whole lot better now.
jgb
-
RE: An SP newbie, trying to write a tutorial.
@cphillips said:
Curbs, dude, you do a hell of a job at explaining hard things.
I absolutely concur!
jgb -
RE: [SP2]Basic Tutorial Posted (Moved & Improved) 5/11/08
I too did it (intuitively) with the joint first attached to the stationary object. I had much difficulty getting things to work.
Since Chris's note on doing it "the other way", I've had more success.
I now look at joint attachment as......
Put the joint on the part that moves, attach and group it in, and then attach it to the other part. ie: Hinge on the door first, then connect it to the door frame.
I also find this also makes editing the setup easier.
And, those newer joints Chris mentioned above seem better. Gotta experiment my Landing Gear model with them.
jgb
-
RE: An SP newbie, trying to write a tutorial.
Curbs,
What you did is great
The presence of the outer skin and door were not part of my first attempts to hinge the bogie to the crank. So at that point I had no problem pushing the bogie through a hole, but that lesson is now understood.
However, I noticed you set the skin state to ignore, to account for the bogie interference. When the drag struts are in place, the bogie will not interfere with the skin. That is part of why I needed motion control on this design to see such interactions. I would change the door opening to suit the bogies motion, and maintain the ignore state, rather than breakup the skin into 4 groups to leave a hole. Reduces model complexity.
Oh, and I know the wheels are square. I have no intention of rotating them, so they can stay that way.
When I first added the hinge to the bogie, and linked it to the crank, it all seized up. I now see that I failed to group the hinge AND the bogie, after attaching the hinge. I thought the joint connector tool did the attachments complete.
The tutorial should include a section on grouping related to joints. What to group, and when. I am still not clear on that concept. I see the crank works yet its servo is not grouped with the crank group. But the bogie hinge had to be grouped to the bogie group to work properly.
So, please correct me if I'm wrong, or left stuff out, but I see the following steps to creating a set of linked objects.
- Create the model with each linked object in the chain as separate groups. Use layers to control visibility.
- Set the object shape that best matches each part. Make sure things that are not to move, but interact with moving parts are defined as staticmesh (not exclusively, but seems best overall).
- Take the first MOVING part1 adjacent the static part (ie: a moving wheel on the static car body) as a group, and connect a joint to it.
- Using the joint connector, lock the joint to the moving part1. Then link the joint to the static part. This is also consistent with Chris Phillips revised way of linking joints.
- Group the joint and the moving part1. (the part I didn't do)
- Test it.
- Attach a joint to the next moving part2 in the chain.
- Using the joint connector, lock the joint to the moving part2. Then link the joint to the previous part1.
- Group the joint and the moving part2.
- Test it.
- Repeat 7-10 for the rest of the chain.
The gyros are a nice touch. Hadn't thought of that to keep the motion civil, before I make the drag links. But why do they stay static and not move with the bogie?
Now I will modify my copy and try to add the drag struts and door linkage. Future enhancements include a controlled sliding joint on the vertical strut to model the Oleo Strut shock absorber. Right now the bogie is modeled with the strut compressed for the retracted position. When the LG is lowered, the Oleo will extend and pressurize to absorb the landing shock.
Thanks again;
jgb -
RE: An SP newbie, trying to write a tutorial.
Thanks, LilDood
I'll check into that, but the real problem is I cannot functionaly link the bogie to the crank with a hinge. When I do, the bogie just hangs from the hinge and blocks the crank from moving.jgb